VICARBO® is carbon-fiber reinforced, in which the carbon fibers are aligned with the longitudinal axis of the material. In this way, we can achieve enormous strength. Thanks to the production process developed by ZERAMEX®, the carbon fibers are not damaged during production and they retain their full function. This screw, for which a patent is pending, is unique in dental implantology!
The VICARBO® screw is a precision screw to optimally capture occlusal forces. When tightened, it grips the existing contour of the thread thanks to the significant different hardness of the ceramic and screw.
- Continuous longitudinal carbon fibers (CF) running down the length of the screw
- Modulus of Elasticity: >160 GPa
- Flexural strength: >1100 MPa
- Tensile strength: 2000 MPa
- Biocompatible per IS010993
ZERAMEX® uses a patented carbon fiber screw which acts as an internal connection and provides the ideal torque on insertion so that the implant can be screwed in without stress peaks being exerted on the bone.
Zeramex Zirconia Implants does NOT have any metal screws nor plastic screws.
The VICARBO® screw is reversible. If anything goes wrong with the crown in the future, you can reverse it.
The screw contains NO GLUE, NO CEMENT.
The material used in making the VICARBO® screw has already proved its worth in other medical applications (e.g. orthopedics) and is considered to be the material of the future. Aerospace engineers also use carbon fiber reinforced components because of their enormous strength and low weight.
Precise anti-rotation protection. These four retaining elements help the abutment to be securely and quickly placed in the implant. The bolt-in tube connection prevents forces being transmitted via the interlocks.
Prevents traction from being exerted on the ceramic. Forces are absorbed by the Vicarbo screw, which functions as a bolt.
Read more about Vicarbo Technology:
Interview F&E Pascal Wettstein – Vicarbo Technology
Carbon – established in dental implantology
Digitization and implantology with ceramic implants is one of the fastest growing and most innovative areas in dentistry. Intensive research and further development in the areas of material properties and restorative care in particular, have led to implants made of zirconium oxide in addition to titanium implants, becoming a serious factor in dental implantology. Dentalpoint with the ZERAMEX® brand is considered a pioneer of “white implants” and launched the groundbreaking ZERAMEX® P6 innovation in March of 2015. A worldwide unique, 100% metal-free, two-piece ceramic implant system with screw connection. The high connection strength required for such a system is achieved by carbon ceramic technology. The core is the Vicarbo screw made of carbon fiber reinforced high-performance PEEK. In the meantime, the further developed system ZERAMEX® XT has already established itself on the market. Representing Dentalpoint with its Zeramex brand, Pascal Wettstein, Head of the Research & Development Department, provides information on what an implant abutment compound is all about and what the future will look like in this matter.
Pascal Wettstein is an experienced R & D engineer with a profound background in materials science. He has been with Dentalpoint since 2014 and part of the great pioneering work. Before joining Dentalpoint, Pascal Wettstein worked for several years as an engineer in the R & D department of renowned Swiss medtech companies.
Mr. Wettstein, ceramic implants are enjoying an upswing in the dental industry. With a current market share of 2-3%, it is predicted that ceramic implant systems will enjoy a market share of up to 25% by 2022. Dentalpoint is a pioneer in this upswing. With what innovation has the ZERAMEX® brand revolutionized dental implantology?
PWE: Historically, in the past, people had a choice between a one-piece and a two-piece bonded implant system, and that’s where ZERAMEX® started. However, we quickly realized that, for reasons of prosthetic flexibility, a two-prosthetic solution is needed. In implantology with titanium implants, virtually no one-piece systems are used anymore, as these are not easy to supply. So our task was clear that even in metal-free implantology you have to offer a system that is reversibly screwed. We were the first to launch a 100% metal-free and two-piece ceramic implant system that is reversibly screwed. This is the great innovation of Zeramex.
The ZERAMEX® systems are known for Vicarbo, a carbon fiber ceramic technology. Why did you choose the material carbon fiber at ZERAMEX®? What are the properties of this Vicarbo technology?
PWE: Fiber composites and especially carbon fiber composites have very special material properties. They have a very high tensile strength (about twice as high as e.g. titanium grade V) and stiffness, they are chemically resistant and they are anisotropic due to the fibers. This means that in the fiber direction you have different properties than transversely. This can be taken advantage of by controlling the fiber course or placing it in the main load direction(s).
A classic example is the bicycle fork made of a carbon fiber composite: it is designed to react elastically to longitudinal loads so that it can optimally cushion impacts, etc. Cross or on torsion it is very stiff, as this massively improves the handling of the bike. With an aluminium fork, it is not possible to control the properties in this mass, as this is an isotropic material (the properties are broadly the same in all directions).
These excellent mechanical properties, combined with low weight, have led to this material being established in a wide range of high-tech industries such as aviation (A380 and Boeing 787), aerospace and racing.
We also make use of the above-mentioned properties. In this way, we build the screw through the process control in such a way that the main fiber curve lies in such a way that it can withstand high mechanical loads on torsion and pull. The combination of a relatively soft screw with the very hard ceramic also allows us to produce the screw in a slight excess. The screw then nestles in the ceramic thread. This results in a sealing effect. The matrix material in our case is PEEK, which has a long tradition in medical technology.
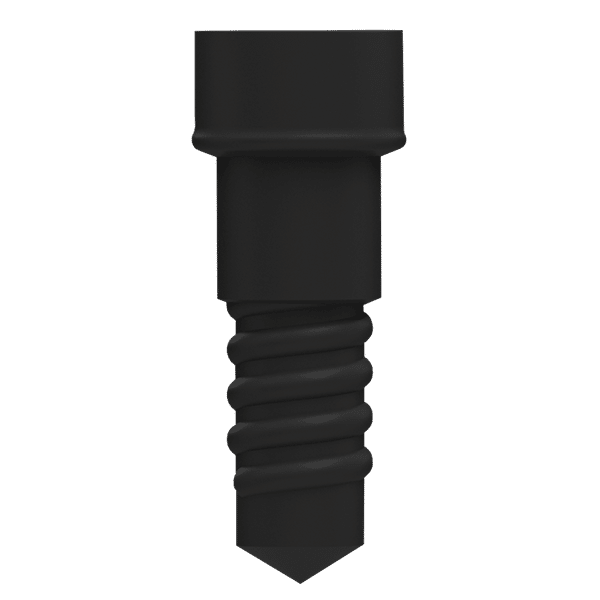
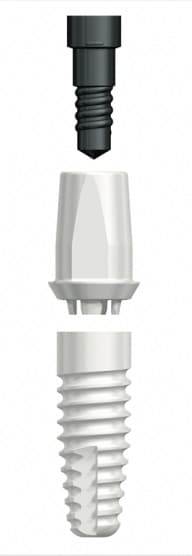
Does carbon find use in medicine anywhere else?
PWE: Yes! The advantages of carbon fiber composites are obvious. The material made of carbon fibers is lightweight, high-stiff, X-ray-transparent and resistant to corrosion – ideal for medtech use. It is already used for bone screws or in “Spinal Cages” and “Cervical Plates” for the surgical treatment of degenerative intervertebral disc diseases. As already mentioned, carbon fiber composites have a higher stiffness than titanium. They also have better fatigue resistance. This is a decisive advantage for high cyclic alternating loads, which occur continuously in spines. The same applies, of course, to an abutment screw, which is constantly exposed to alternating loads due to chewing.
One hears again and again about stability problems with screws of two-piece implant systems. What about the long-term stability?
PWE: Although there are no clinical studies on the Vicarbo screw yet, our five-year data speak very clearly. Information about statistics (So and so much are user errors)
Of course, a composite material, such as Vicarbo, can also cause material failure, such as “fiber pull-outs” or a “matrix delamination”. These are not breaks in the classical sense, but start with a failure of the interface of the PEEK matrix and the carbon fibers, which ultimately leads to a failure of the composite.
As with any screw, care should be taken to ensure that the torque is maintained. In addition, the prosthetic wrench must sit cleanly in the screw drive to ensure optimum force introduction. However, this generally applies to screws and is not limited to the Vicarbo screw.
Based on our market feedback, however, we can say that since the introduction of our Vicarbo technology, the screw has been extremely reliable.
In medicine, studies are always a much-discussed topic and can also provide information on whether a product is ready for the market. Are there any studies on the Vicarbo screw?
PWE: As I said, there are no long-term studies, but we have well-documented five-year data from our market feedback and they look very good. We have very, very few problems with the Vicarbo screw and that makes us very positive for the future. But we can’t conjure up or speed up time: 10 or 20 annual dates are only available in 5 or 15 years. But this generally applies to any new development, regardless of the system.
In order to intercept this, of course, one generates enough data, which allows the conclusion that the materials or system used is stable to the entire long-term. These include artificial aging tests, alternating load tests in various medium or maximum load tests. All these tests showed that the Vicarbo material, due to its unique properties, is very suitable for this application. The values in cyclic stress tests are comparatively very high.
All ZERAMEX® systems currently available on the market are also approved by the U.S. Food and Drug Administration (FDA).
Is there anything special to consider when handling titanium screws?
PWE: Basically not. Our Vicarbo screw is also a simple screw that is inserted by means of a prosthetic key. Because a comparatively soft screw is screwed into a very hard ceramic thread, the haptic feedback is a little different than when screwing two ductile materials such as titanium on titanium. Due to the specific properties of the two materials, our screw connection is also formed as a round thread, which is not found in titanium implants.
What advice would you give to dentists who are uncertain about ceramic implants? In the meantime, other manufacturers have also launched two-part reversible ceramic implnats. In addition to their system, there are, for example, ceramic implants with titanium screws or ceramic implants with ceramic screws. How do you see this personally, what will prevail in the market and what will work?
PWE: Quite simply, the system will eventually prevail, which is the easiest to use and delivers the best results. What system will be revealed? I leave coffee grounds reading to others.
What I can say, however, is that we have been working with Vicarbo for five years. We are very satisfied with the market feedback data and therefore play a decisive role in a very good way in the industry. The fact that well-known companies include our products in their portfolio underlines the confidence in our developments. We can also be proud of that.
As a company, we have also been dealing with ceramics for over twelve years, with a corresponding wealth of experience, setbacks and successes. We have invested a lot in experiments, tests and basic work, tested different compounds and materials to lay a serious and experimentally confirmed basis. Anything else in our industry would also be negligent. The decision to bet on Vicarbo was finally made because we came to the conclusion on the basis of the data that this is the best solution, which optimally complements the very specific properties of ceramics. But let us not forget that new products keep coming onto the market and a lot of clever minds are working on solutions. It is impossible to say what developments, improvements or revolutions are still to come and whether they are capable of displacing existing products. It is always interesting to observe the dynamics in the developments, for us from this field anyway!
Vicarbo® and Zeramex® are trademarks of Dentalpoint AG.
Contact
Want to know more about Zeramex?
Email us at sales@zeramexusa.com with your contact details and we will get in touch with you!
ZERAMEX BROCHURE
Click here to download the Zeramex sales brochure